En el marco del lanzamiento de la nueva generación de camiones, Scania Argentina nos invitó a visitar las instalaciones de su fábrica ubicada en la localidad Colombres, provincia de Tucumán. Esta fábrica, inaugurada en 1976, cuenta con un área cubierta de 41.000 m2 donde trabajan 540 empleados divididos en 4 turnos de trabajo, por lo que funciona las 24 horas del día, los 7 días de la semana.
La planta argentina se especializa en procesos de mecanizado, produciendo componentes de transmisión, caja de cambio y diferenciales, y siendo una parte vital del sistema de producción global de la marca.
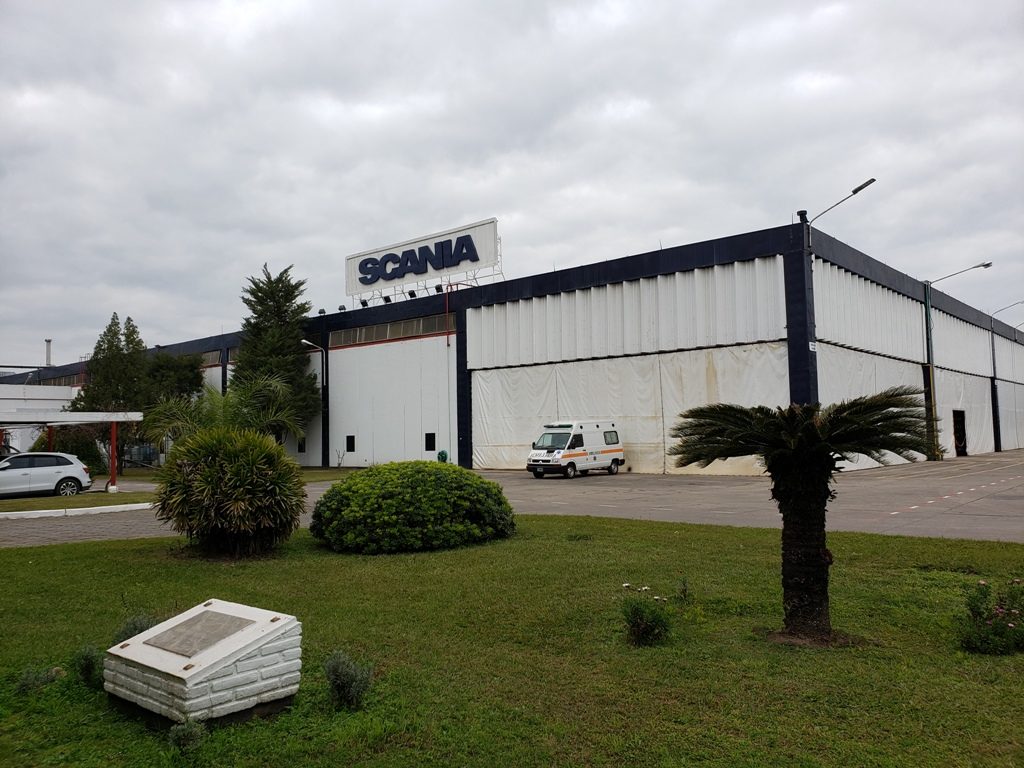
Actualmente, cuenta con once líneas de producción, con equipamiento de última generación y procesos que aseguran el mismo nivel de calidad que en la casa matriz en Suecia. Se producen 30.000 cajas y 40.000 diferenciales al año, exportándose la totalidad de la producción a Brasil y Suecia.
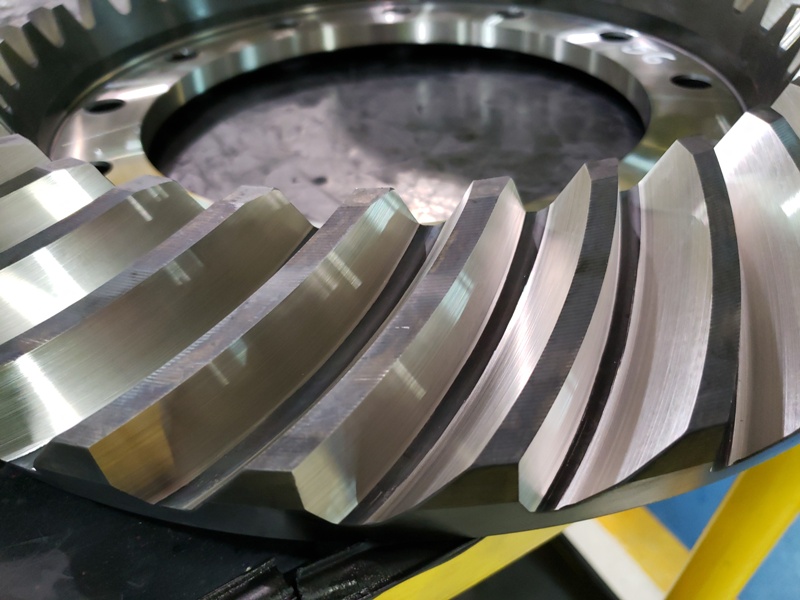
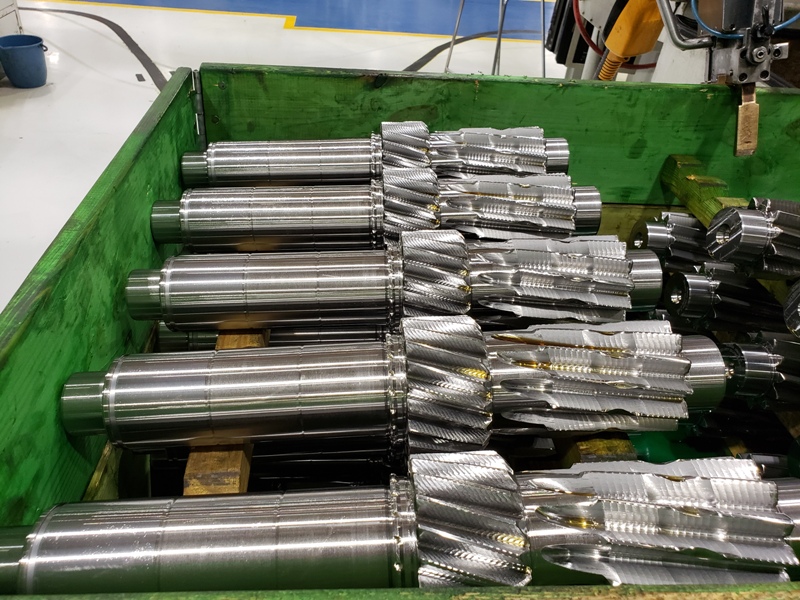
Una de las premisas de la fábrica es la Sustentabilidad y el cuidado del Medio Ambiente, por lo que los desechos de los distintos procesos de producción son reciclados para reducir el impacto medioambiental. De esta manera, Scania está fijando objetivos a corto y largo plazo para cumplir con estos compromisos; en la actualidad, se está modernizando el sistema de iluminación de la planta fabril por iluminación LED, lo que se traduce en un ahorro de energía del 10%. A su vez, se utilizan soluciones sintéticas y aceites biodegradables que se reutilizan en nuevos procesos productivos. Además, la fábrica cuenta con su propia planta para tratamiento de efluentes.
Cabe destacar que la marca Sueca realizará una importante inversión entre 2019 y 2020, de unos 35 millones de dólares, para mejorar la eficiencia de los procesos productivos, la renovación de maquinaria y tecnología y la capacitación de su personal: se incorporó nueva maquinaria que permite el corte en seco de las piezas, eliminando la utilización de lubricantes refrigerantes durante el mecanizado, como así también maquinaria para el rectificado de Corona y Piñón y de engranajes.
Durante el recorrido, nos mostraron los distintos procesos a los cuales se someten las piezas, desde el ingreso de la materia prima, siguiendo por los procesos de corte y mecanizado, como así también el tratamiento térmico de los componentes que consiste en calentar las piezas en hornos hasta temperaturas cercanas a los 1000° C, que luego son enfriadas repentinamente en aceite para fortalecer el material. Otro de los procesos de suma importancia es el “Shot Peening”, que se basa en el “bombardeo” de granallas (cut wire) para limpiar e incrementar la resistencia a la fatiga de las piezas.
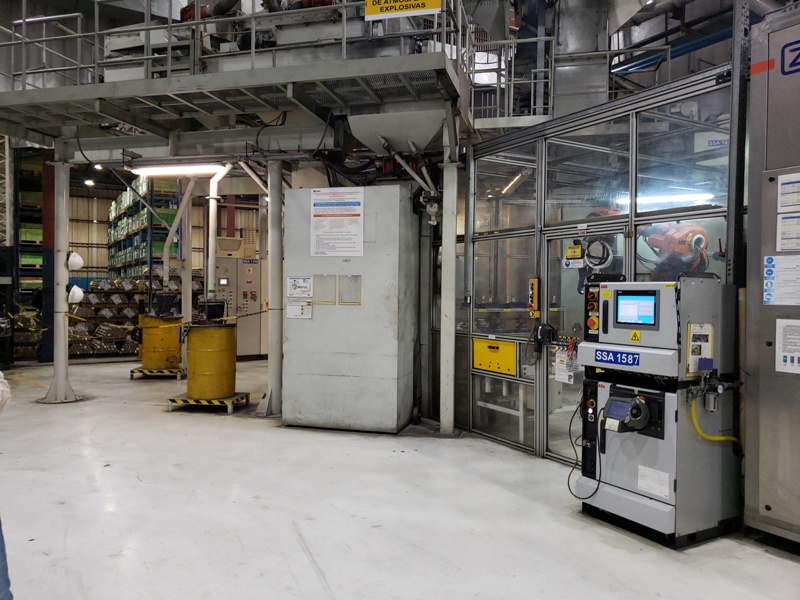
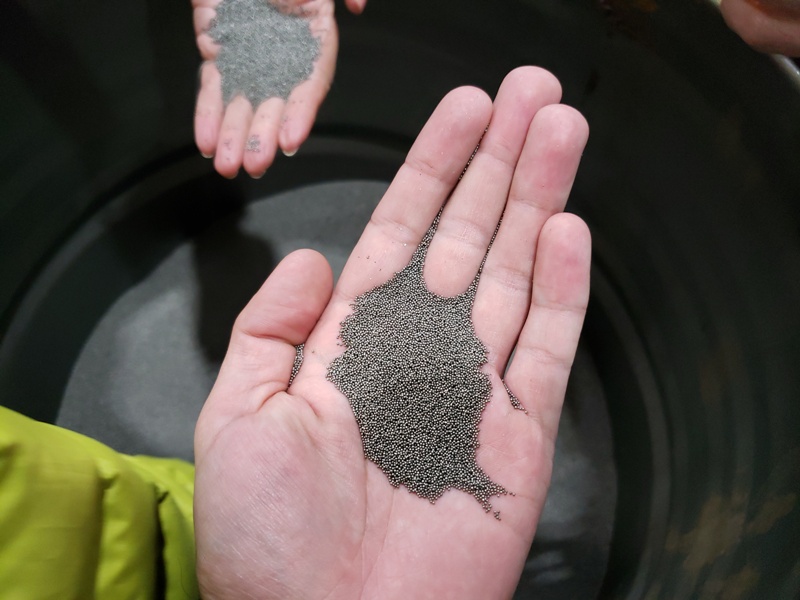
Para el transporte de piezas en el interior de la planta, se utilizan autoelevadores a combustión (reemplazados paulatinamente por autoelevadores eléctricos en virtud del compromiso de Scania con el Medio Ambiente) y los denominados AGV (Automatic Guided Vehicles) que son vehículos autónomos que recorren las instalaciones de la fábrica transportando piezas en los distintos procesos. Su utilización proporciona no sólo una reducción de costes y un aumento en la eficiencia de los procesos, sino también mejoras en seguridad y en calidad, optimizando, a su vez, la ergonomía de los operarios.
La fábrica de Tucumán cuenta, además, con una Sala de entrenamiento para Percepción de Riesgos para que los operarios sepan anticipar riesgos y evitar accidentes. A su vez, Scania Argentina capacita al personal en áreas de producción, medio ambiente, uso de herramientas y mantenimiento, como así también control de calidad.
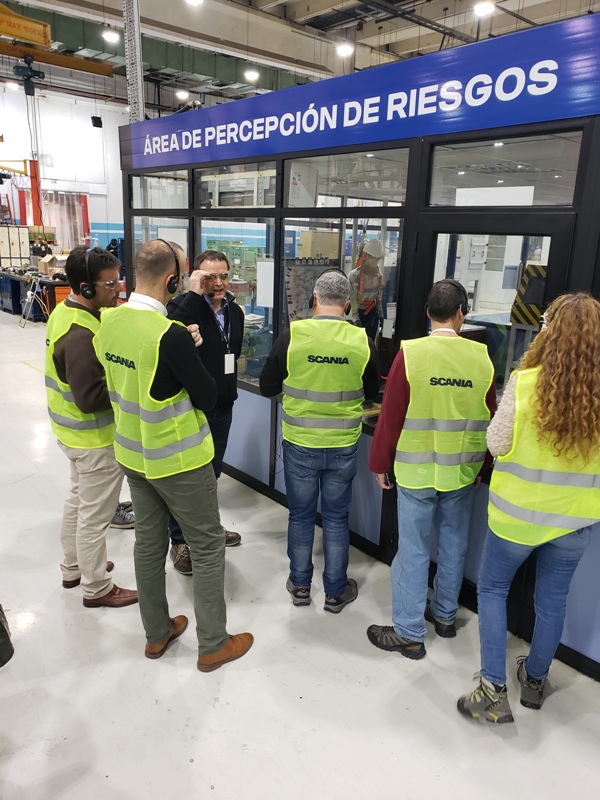